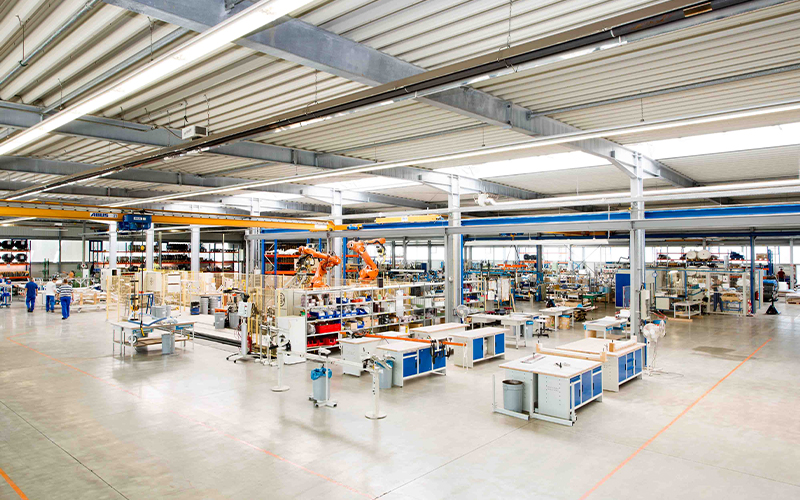
Digitalization of Production and Logistics at Partzsch Spezialdrähte GmbH
Always on the ball for customers
At its Ossig location in Saxony, Partzsch Spezialdrähte GmbH annually manufactures approx. 7,000 tons of copper and copper flat wires for generators, transformers and electric motors – both for the Partzsch Group of Companies and for customers in the electrical industry. The aspiration: to always be on the ball for their customers through comprehensive know-how, a high degree of flexibility and short delivery times. Previously, all processes, from goods receipt to production and goods issue, were managed on paper. The innovative company expected that digitalization would improve information flows and provide greater transparency regarding inventories, order status or minimum shelf life – and thus enable more efficient production control, seamless tracking of materials and components, and increased profitability in the use of resources. To maximize the impact, it was decided to synchronously advance the digitalization in the flow of materials and information for production and logistics in a pilot project.
Driving digitalization forward with a competent partner
LOGSOL was brought on board in 2021 to analyze the maturity level of digitalization, create a target concept, including prioritization and derivation of a roadmap, and for joint implementation.
In the first step (beginning of May to the end of July 2021), the LOGSOL project team conducted a full-scale actual-state analysis of all relevant processes to derive the maturity level of digitalization on a uniform data basis. Core processes and information flows were documented and visualized for the following areas: goods receipt and intermediate storage, production, finishing, finished goods storage and goods issue, administrative processes, production and logistics. In addition, the performance of the existing IT system (including system interruptions) was examined and other relevant influencing factors were included. In the second step, the LOGSOL planning specialists conducted a potential analysis together with the customer to identify the most effective approaches and solutions and combine them into a target vision. The resulting measures were clustered and prioritized according to their benefits and implementation costs, so that a schedule could be recommended for their step-by-step implementation.
High speed despite industry-specific challenges
“The speed of the actual-state analysis was a project highlight for me”, describes Andreas Zorn, Business Operations Manager at Partzsch Spezialdrähte. “All processes were independently recorded directly on site by a LOGSOL project manager within just three weeks and subsequently mapped perfectly in a process tree. Furthermore, digitalization potentials were well identified and highlighted. I was very impressed by the project manager’s rapid understanding of our very complex, specific interlocking processes in copper production in such a short time. That’s because the devil is in the details: the subject of copper was new to LOGSOL and involved special requirements. Bringing everything together in our ERP system in a cost-efficient, targeted and future-oriented way is also a major challenge.” Furthermore, the division of the project into ten pragmatic work packages, which took into account the given dependencies in their chronology, was particularly impressive. The strong target concept, full-scale roadmap and a detailed estimate of the effort required to implement the individual work packages became the basis for the decision for this investment – and for the joint path with LOGSOL.
Embarking on a journey together
In April 2022, LOGSOL was commissioned to implement the first four work packages. The entire package is to be completed by the end of 2023 with the connection of the entire production facility.
“Our goal is to always create the best possible processes for our customers and implement these together with them rather than merely developing concepts and showing the customer the corresponding potentials and options. That’s why we are very pleased that we are now implementing the first four work packages together with the Partzsch Spezialdrähte team”, says Carsten Gutmann, responsible Senior Logistics Planner at LOGSOL. “The joint constructive cooperation is very motivating for us and it is the specialty of this project. Everyone wants to synchronize the flow of information and materials, so they are all playing their part and working together. There is very open communication and the issue is being pushed forward by the management down to the production staff.”
Digitalization as an opportunity – especially in challenging times
“With the currently extremely volatile high prices for energy and copper, both of which are traded on the stock exchange, it is only possible to act at very short notice in terms of prices, both on the supplier and customer side. Through synchronous digitalization of the material and information flow for production and logistics, we receive real-time data very quickly, e.g., for determining demands. In addition, we know exactly which material we need on which day and can order accordingly with precision, thus reducing expensive inventories. With a copper market price of 9 EUR per kilo and an annual production of 7,000 tons for example, every reduction in inventory is worth a lot of money. In general, the market is becoming increasingly fast-paced and complex. Thus, controlling production and logistics with real-time data and key figures is essential and extremely important, also and especially if you want to maintain or expand your market position”, says Andreas Zorn, summarizing the advantages of digitalization for Partzsch Spezialdrähte.
Further joint projects for the Partzsch Group of Companies
The LOGSOL team has obviously succeeded in proving that LOGSOL can be a strong partner: digitalization in production and logistics at Partzsch Spezialdrähte GmbH was LOGSOL’s first project for the medium-sized Partzsch Group. Already, one of its sister companies, Partzsch Elektromotoren GmbH, has decided to take advantage of LOGSOL’s experience in the areas of material and information flow and digitalization projects and involve the team in the upcoming process optimization.