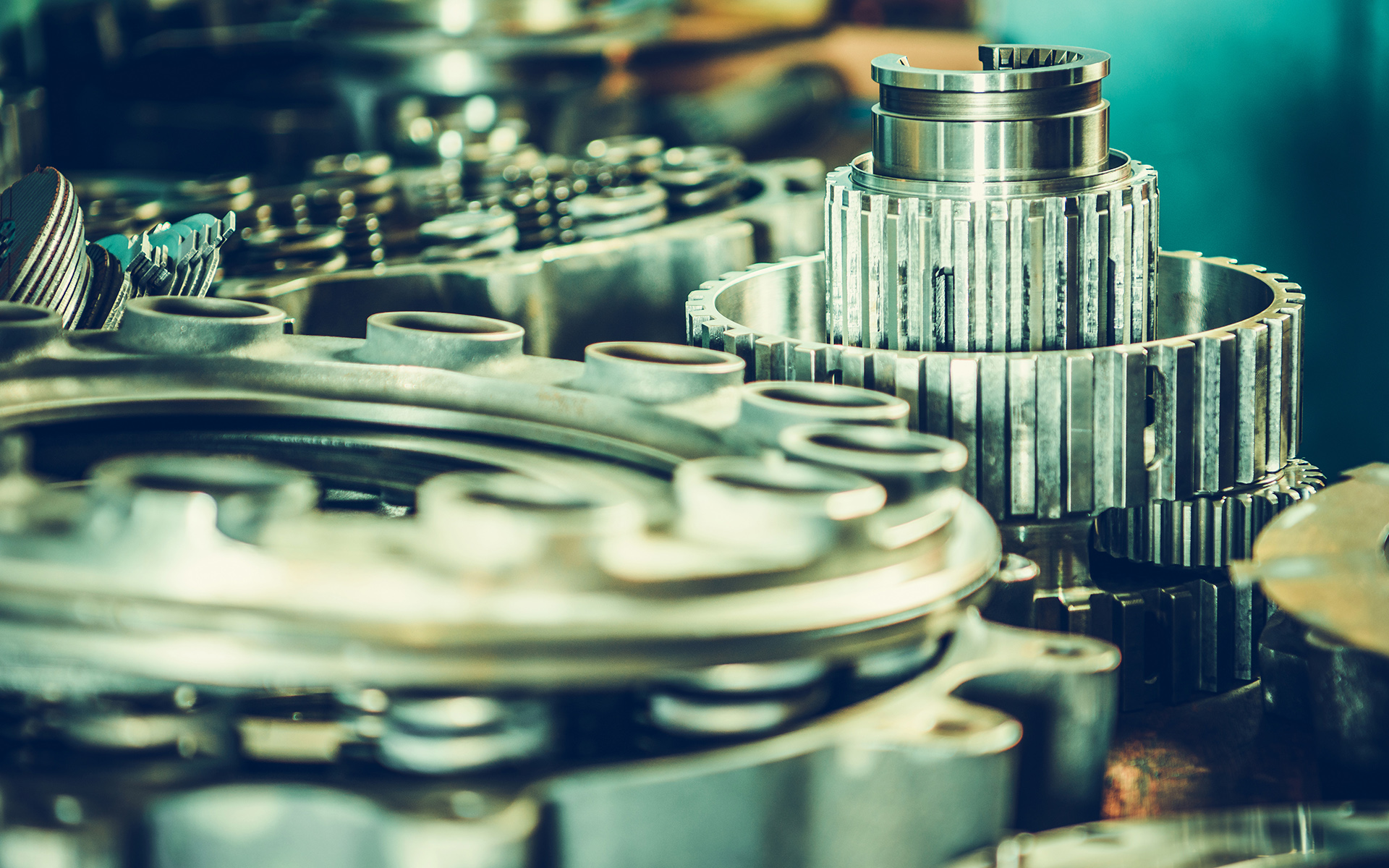
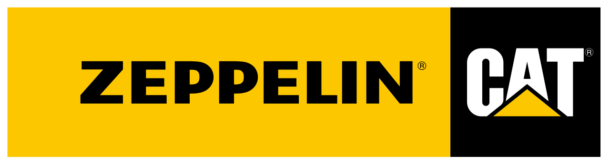
Container management: conserving resources and saving costs
Zeppelin Baumaschinen GmbH specializes in the sale, rental and servicing of construction machinery. They offer a wide range of construction machinery and equipment for various industries and applications.
The project
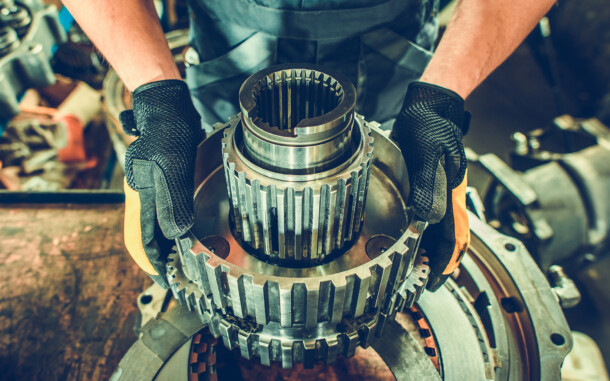
As an exclusive partner, Zeppelin Baumaschinen GmbH has been ensuring the availability of spare parts for Caterpillar construction machines at the central spare parts warehouse in Cologne for over 50 years.
Reduction of transport damage
The objectives of flexible load carrier management systems are being pursued with vigor. The background to the introduction of the BinMan® container management system in one of the world’s largest construction machinery trading organizations included criteria for securing loads, conserving resources and saving costs. In particular, the reduction of transport damage and better weather resistance of the packaging spoke in favor of using reusable containers with individual barcode labeling instead of vulnerable disposable packaging.
The implementation
Specification and structuring phase
Based on a specification workshop and the requirements communicated by Zeppelin Baumaschinen GmbH, LOGSOL created a solution proposal for mapping all requirements in BinMan® 2.0. The customer’s focus was particularly on real-time individual container tracking and the integration of mobile data collection devices.
Realization phase
In addition to the classic view on the PC, BinMan® is also available as a mobile version for the Falcon X3 handheld used at Zeppelin. For this purpose, the user interface on the scanner devices integrated into the system via WLAN was customized to the operational processes of Zeppelin Baumaschinen GmbH. The focus here was on simple and intuitive operation of the devices during operations. Master data views and evaluations for the mobile devices were completely dispensed with in order to keep the booking effort as low as possible.
Further focal points in software development:
- Extension of BinMan® for tracking individual containers (container master data, stock overviews, inventory functions)
- Option for quick creation of individual containers
Test phase
- Provision of a QA test system
- Automated, browser-based test runs
- Model-driven software development
All software developments were extensively tested for full functionality/usability by the customer’s project managers and LOGSOL in the QA system provided and approved by the client. Additional solution approaches were also developed, which were specified later in the project and fully implemented for the client.
The results
Introductory phase and go-live
During the introductory phase, the key users at Zeppelin Baumaschinen GmbH received personal on-site training in Cologne. LOGSOL also provided the individual database and the separate domain for the client. Since the successful go-live, Zeppelin has had a help desk system and a support hotline at its disposal.
Currently, up to 400 container movements are recorded daily by employees in two-shift warehouse operation and booked in real time.
Download all the important information about BinMan® here.
Relevante Fachbereiche
Would you like to find out more about our services?