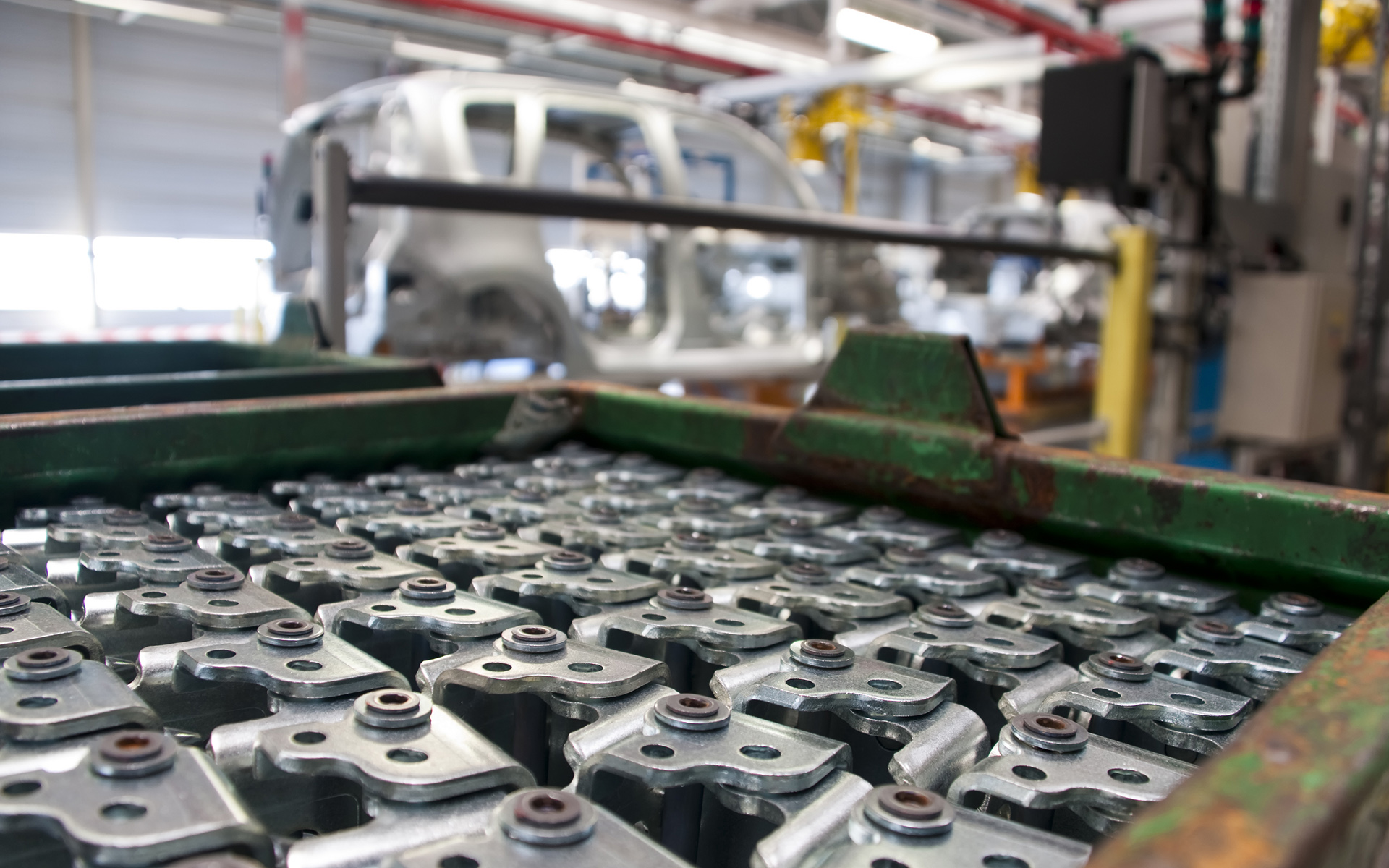
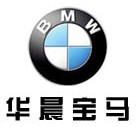
Efficient container management at BMW Brilliance: empties planning with BinMan®
BMW Brilliance (officially BMW Brilliance Automotive Ltd.) is an automobile manufacturer headquartered in Shenyang, China, and a joint venture between BMW (as majority owner) and Brilliance Auto. The main activity of the company is the production, distribution and sales of BMW passenger cars in mainland China.
The project
BMW Brilliance Automotive Ltd (BBA) uses BinMan® for container monitoring. BinMan® also supports BBA in the planning of empties deliveries by means of a dynamic shipping quantity calculation based on actual demand data. To this end, the standard solution of the cloud-based container management system was tailored to the customer’s individual requirements profile.
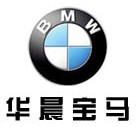
Compared to other similar software products, BinMan® is an intuitive and easy-to-use software that can nevertheless effectively and completely map all the requirements of BMW Brilliance Automotive Ltd.
Joe Dong,
Project Manager Logistics, BMW Brilliance Automotive Ltd.
The implementation
Specification and structuring phase
Based on the specifications provided by BBA, LOGSOL drew up a detailed requirements specification. In addition to the requirements specification, additional optimization approaches were also mapped by the LOGSOL product managers. The adjustments were finalized and approved in a joint workshop on site in China. The customer’s focus was on a practice-oriented, on-time implementation of the adjustments.
Realization phase
Some functions of the standard BinMan® software were adapted to the requirements, but the focus was on the development of new functionalities.
Focal points in software development:
- Empties shipping calculation based on SAP production data
- Expansion of master data regarding material allocation, fill levels and transport time as the basis for shipping calculation
- New process for handling complaints
- Customized inventory processing
- Possibility of mapping container scrapping and repairs directly in the system
Another challenge was the provision of the entire system in Chinese.
Test phase
- Provision of a QA test system
- Automated, browser-based test runs
- Model-driven software development
All software developments were extensively tested for full functionality/usability by the project managers from BBA and LOGSOL in the QA system provided and approved by the client. Additional solutions were also developed, which were specified and fully implemented by LOGSOL later in the project in accordance with the standardized change request process.
The results
Introductory phase and go-live
The standardized project process enabled a smooth introduction at BMW Brilliance Automotive Ltd. with a timely go-live of BinMan® on site in China. In compliance with the individual rights concept, the user accounts were activated on schedule, accompanied by extensive user training for employees and suppliers in Chinese by the LOGSOL project team. The start-up of the system and a 4-week start-up support were successfully accompanied by a LOGSOL expert on site in China.
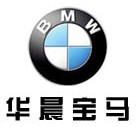
The various functions of BinMan® have enabled us to make the use and management of our containers much more effective and efficient. We now have transparency of all container stocks along the entire supply chain at all times. Our expectations have therefore been fully met.
Joe Dong,
Project manager, BMW Brilliance Automotive Ltd.
Download all the important information about BinMan® here.
Relevant specialist areas
Would you like to find out more about our services?