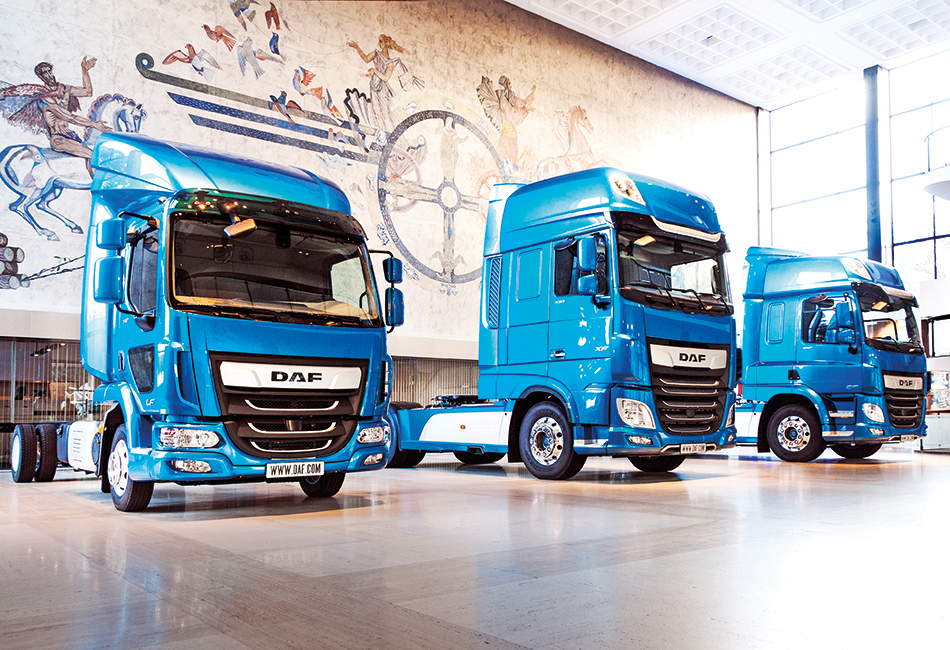
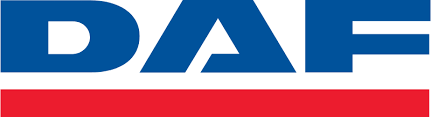
Digitalized container management system at DAF Trucks: Mobile data acquisition with BinMan®
DAF Trucks N.V. is a Dutch manufacturer of light to heavy commercial vehicles, which is part of the PACCAR Group - one of the world's leading commercial vehicle manufacturers. The company's three model series (XF, CF, LF) are tailored to customer requirements.
The project
Based on a specification workshop and the requirements communicated by DAF Trucks N.V., LOGSOL created a solution proposal for mapping all requirements in BinMan® 2.0. The customer’s focus was particularly on the real-time tracking of individual containers and the integration of mobile data collection devices.
The implementation
Returnable load carriers are playing an increasingly important role in production companies. LOGSOL GmbH was commissioned to implement a company-wide container management system (BMS) at DAF Trucks with the aim of knowing where, in what quantity and in what condition the company’s containers are located. During workshops lasting several days on site in Eindhoven, the headquarters of DAF Trucks, the customer’s specific requirements were defined together with LOGSOL’s specialists.
The requirement criteria included the following points:
- Dynamic minimum and maximum stock calculation based on historical values
- Customer-specific outbound process incl: Creation of transport orders in the BMS as well as automatic transmission of these to and confirmation by the DAF transport management system (TMS) and mobile recording of empties transports via tablet directly during loading
- Customer-specific inbound process incl. complete integration of BinMan® into the DAF Trucks IT infrastructure for the exchange of notification data (ASN) and mobile recording of the delivered load carriers directly at the unloading ramps as well as direct comparison with notified load carrier types and quantities
The customizing and introduction of the system at the various locations was carried out in four phases within a project duration of just 10 months. With the support of LOGSOL, it was possible to standardize and almost completely digitalize the different processes at the production sites. The main focus is on the increased automation of booking processes, which are now only checked and validated in the system by employees using mobile devices (tablets) on a random basis. In addition, the focus was on efficiently managing the supply of empties from suppliers using the pull principle.
The results
Introductory phase and go-live
With the initial go-live in phase 1 at the end of 2016, the standard functions of BinMan® were successfully rolled out at all DAF Trucks locations. The new outbound process was successfully implemented in phase 2.
The digitalization of the processes was then further advanced by the adapted inbound process in phase 3 (also based on the use of tablets). In addition, all DAF Trucks suppliers were trained by LOGSOL GmbH project managers and specialists in the third implementation phase. Since then, more than 500 suppliers have been ordering their returnable load carriers from the Dutch commercial vehicle manufacturer via the LOGSOL BinMan® container management software and are actively using the new system to record and check container movements.
In subsequent milestones, the focus was on customer-specific requirements for the complaints process and the expansion of the integrated evaluation tools and reports. As a result, the control and management of returnable load carriers at DAF Trucks was made even more efficient and adapted to the individuality of the customer.
Download all the important information about BinMan® here.
Relevant specialist areas
Would you like to find out more about our services?